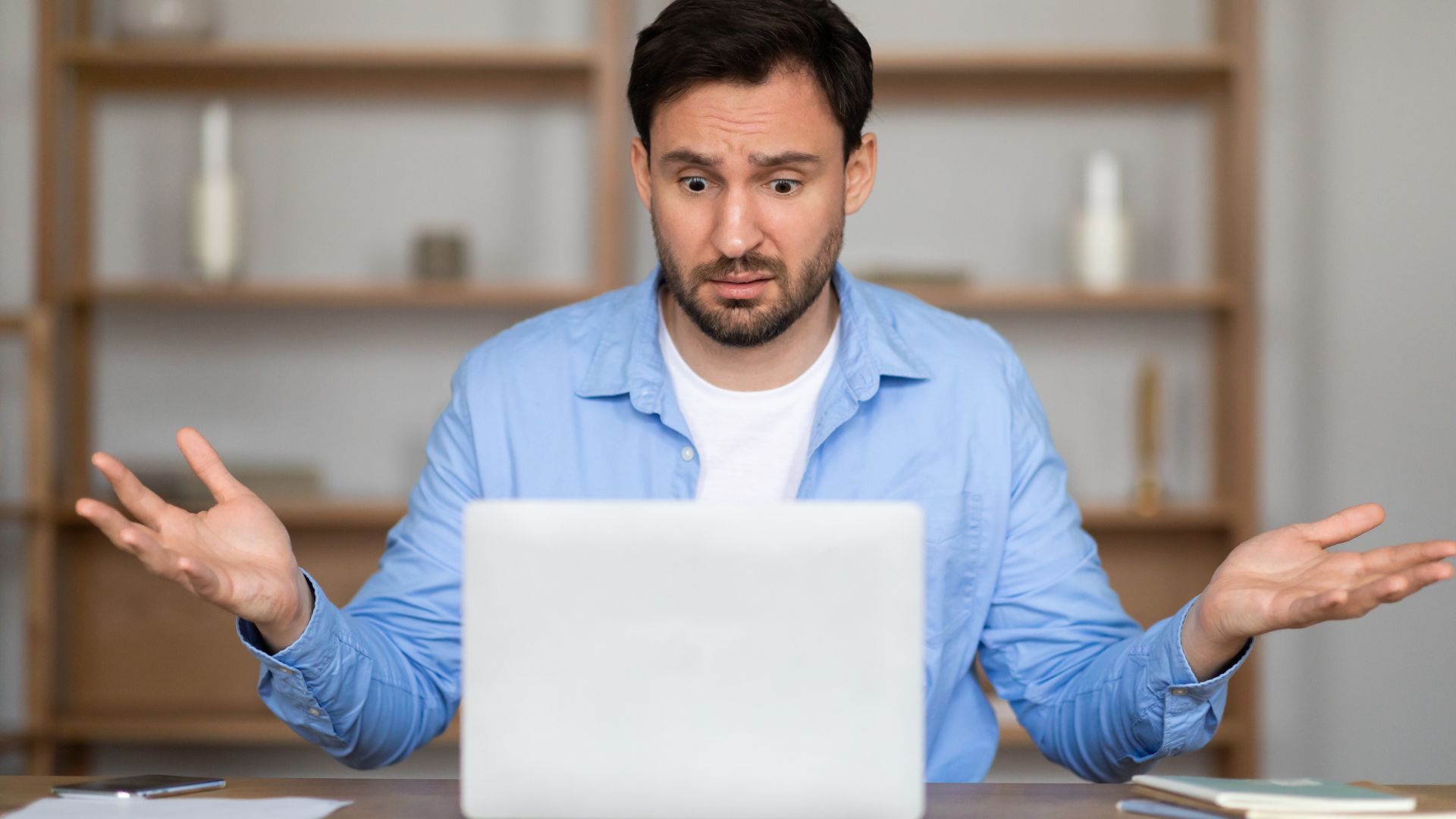
Do your overseas suppliers speak your language? No, we’re not talking about whether they can pronounce “aluminum” the American way. We’re talking about the more complex communication that keeps your production lines running, your costs in check, and your reputation intact.
When companies work with overseas manufacturers, things don’t always go according to plan. Sometimes, it’s a misinterpreted email. Other times, it’s a shipment that mysteriously disappears between “on the way” and “where on earth is it?” You don’t need to be fluent in Mandarin, Vietnamese, or Bengali to manufacture globally. But you do need someone who can bridge the gap linguistically, culturally, and logistically.
Let’s explore the not-so-glamorous (but very real) global manufacturing challenges that businesses face and how a savvy partner like ITI Manufacturing turns those headaches into high-fives.
When Communication Goes Sideways
One of the most common (and maddening) global manufacturing challenges?
Miscommunication!!!
Ever played the telephone game as a kid? Imagine doing that with $500,000 of production parts and thirteen different time zones. Words get lost. Meanings get twisted. And the next thing you know, you’ve got a cargo container of parts that almost meet your specs.
Even basic business terms can cause confusion. What you call a “purchase order” might be interpreted differently by a factory overseas. Without a clear understanding of processes, documentation, and expectations, small errors can snowball into production disasters.
Now, you could spend years studying foreign languages and supply chain theory, or you could work with someone who already speaks the language. At ITI Manufacturing, we work directly with overseas factories using bilingual project managers who live where the factories operate. These folks aren’t just translators; they’re fluent in manufacturing, too. Which means? It means we know how to read a spec sheet and a situation. Huzzah!
Why “Good Enough” Should Never Be Good Enough
Let’s be honest: If you’re ordering 50,000 parts from across the globe, you expect them to be right the first time. Not almost right. Not right-ish. But right, right.
Well, here’s a fun fact: Many companies don’t realize there’s a problem with their product until it’s already sitting in their warehouse or, worse, in their customers’ hands. Now, you’re dealing with rework, returns, and reputational bruises—ouch!
How do we solve this hiccup? Proactive, not reactive, quality control.
ITI has boots on the ground inspecting product quality before it leaves the factory floor with our Proven Process. Think of us as the bouncers at the club of your supply chain—nothing gets past us unless it meets the specs. And if there’s a hiccup? We catch it early, work with the factory to resolve the issue, and keep you looped in on the progress. No surprises. No finger-pointing. Just solutions. How do you like that? (Because we kind of love it! It’s all about customer satisfaction at ITI.)
Time Zones, Holidays, and Other Things That Make Shipments Late
Time is not just a construct. It’s a logistical nightmare when you’re dealing with suppliers around the world. Maybe your team in the United States emails a supplier at 3 p.m. on a Wednesday. But it’s 4 a.m. Thursday in China and it’s a holiday and it’s one you didn’t even know existed (insert exaggerated sigh here). You finally get a reply on Friday, but by then, you’ve lost a whole workweek.
These kinds of delays aren’t just annoying, they’re costly. And when you have to explain to your customer why their delivery is delayed? Not fun.
With ITI’s team physically located in the countries where production happens, you get 24/7 problem-solving. We know when holidays are coming—all of them. We understand local customs. And we’re on-site to keep production moving while you’re cozy in bed. (It’s okay, you don’t have to say it. We already know we’re awesome.)
Contracts and Currency and Culture, Oh My!
You’ve nailed down pricing, signed the contract, and sent the deposit. Great! But what happens if the factory switches materials to save money? Or the exchange rate tanks? Or someone misinterprets a contract clause? This is where many companies find themselves knee-deep in spreadsheets, scrambling to figure out what went wrong.
But at ITI? We’ve been down this road. We help our clients navigate these not-so-small details with precision. Our team verifies the materials used, watches for currency fluctuations, and ensures your contract terms are followed exactly. Don’t worry, we’ll guide you up the mountain without letting you fall into a crevasse made of shipping delays and budget overruns. In a nutshell? We’ve got your back!
The Myth of the “Set It and Forget It” Supply Chain
If you think you can just place an order with an overseas factory and wait for magic to happen, we have some unfortunate news. There’s no “Easy Button” for global manufacturing. It’s complex. It’s dynamic. And if you’re not paying attention, it’ll sneak up and cause problems faster than you can say “delayed shipment.”
International manufacturing success isn’t about luck. It’s about preparation, people, and proactive problem-solving. At ITI Manufacturing, we have built our business around doing exactly that.
We don’t just step in when things go wrong. At ITI Manufacturing, there is no such thing as, “Set it and forget it.” We set things up with you directly and right from the start: defining expectations, building checkpoints, communicating with you weekly, verifying quality, and managing supplier relationships so you don’t have to.
Don’t Handle Global Manufacturing Alone
If global manufacturing were easy, everyone would be doing it flawlessly. But the truth is, even big-name companies stumble when they don’t have the right systems or the right support in place.
Manufacturing overseas is just too much for anyone to handle alone. Get a quote from one of our pros today!