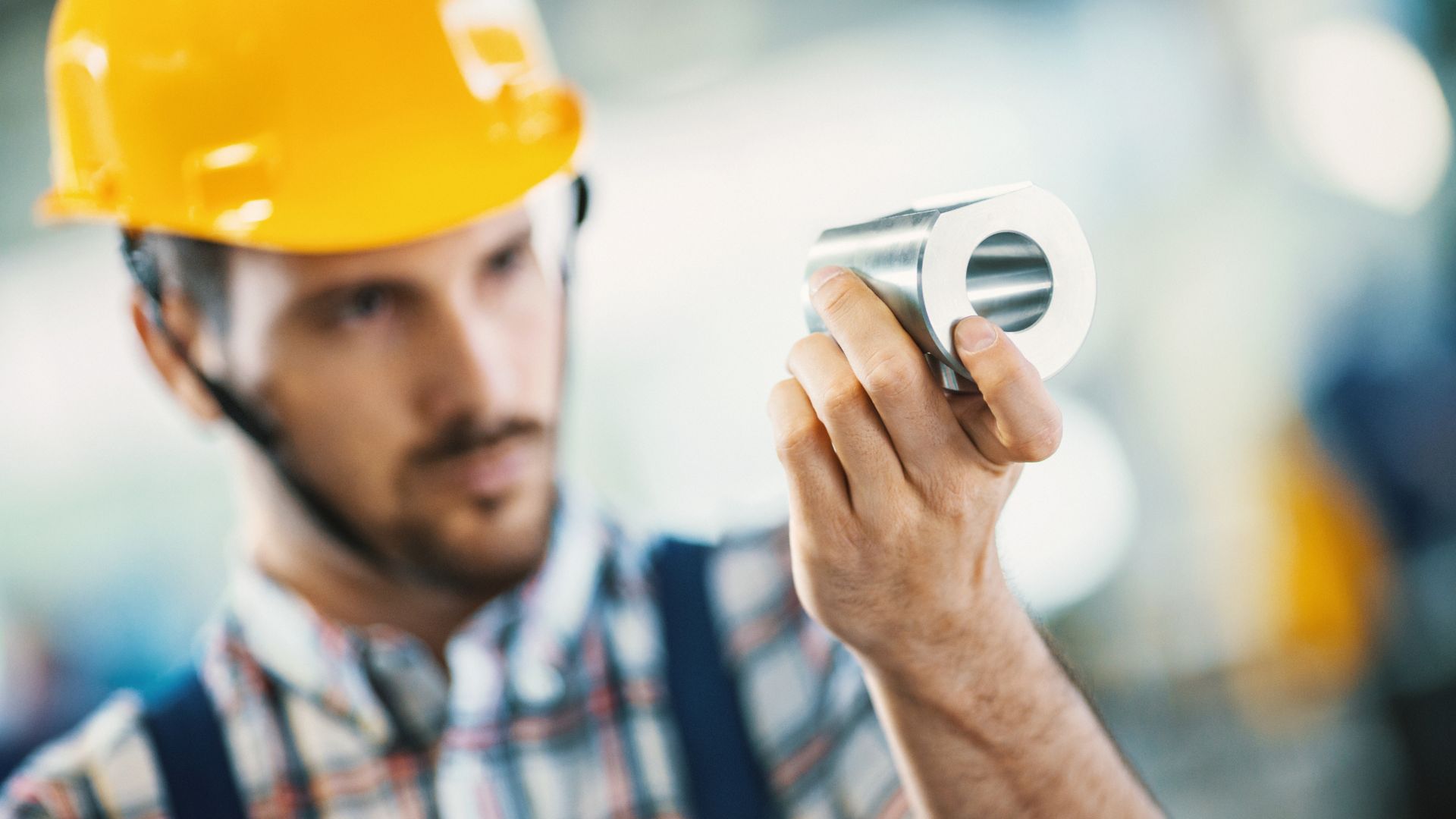
In the domain of industrial product sourcing, the word “quality” is tossed around constantly. Here we discuss quality as it relates to component manufacturing, and outline methods that buyers can use to ensure high quality in their manufactured products.
Let’s start by considering that quality means different things to different people. Product designers may measure quality by appearance and aesthetics. Engineers might consider quality to mean technical and functional performance. End users often consider quality in terms of cost and lifespan. At the end of the day, each of these examples (and more) would be correct, making quality management all the more critical.
Let’s start with a definition.
Quality in Component Manufacturing
With industrial component manufacturing, what exactly do we mean by the word “quality”? To answer this, let’s take a look at the gold standard for quality management system (QMS) requirements, recognized around the world as ISO 9001. ISO 9001 is part of a family of standards that set the bar for QMS programs, which are business processes that companies use to specify, implement, manage and audit their operational practices. Companies use ISO 9001 as the guidance document to generate their own QMS, which can then be certified as in compliance with ISO 9001 requirements. Using an ISO 9001-compliant quality management system offers these four benefits:
- Enables the ability to consistently provide products and services that meet customer and applicable statutory and regulatory requirements.
- Facilitates opportunities to enhance customer satisfaction.
- Addresses risk and opportunities associated with its context and objectives.
- Provides the ability to demonstrate conformity to specified quality management system requirements.
From the above, if a QMS’s goal is to enhance customer satisfaction and address risk, then quality itself must be whatever tangible features of a product, transaction or user experience lead to customer satisfaction and sufficiently minimize risk.
Aligning QMS Expectations With Manufacturers
Expecting high-quality products from contract manufacturers is one thing: Explicitly defining and then ensuring high-quality output is quite another. At multiple steps along the path of engaging manufacturing services, buyers must continuously evaluate a vendor’s commitment to quality, and seek alignment on what that commitment entails.
The spectrum of quality parameters in component manufacturing ranges from highly subjective to highly technical, and is worsened by language barriers, communication challenges and perspectives on the involved costs. This is where a well-established quality management system can pay dividends.
Buyers can seek out manufacturers that are ISO 9001 certified or that have a QMS certified to another recognized standard. In addition, buyers can write out their requirements to provide to manufacturers, helping align both parties to a central set of expectations. ISO 9001 includes the following set of seven quality management principles that can help buyers generate their expectations.
- Customer focus: This principle of quality management puts both internal and external customers at the center of the equation. Buyers can write out the expectations that their end-users will have of the products being made, making the manufacturer aware of critical factors that will be measured in terms of quality.
- Leadership: Ensuring that quality expectations are met takes fortitude and willingness to push through obstacles in pursuit of high quality. Buyers must write and communicate their expectations from a position of leadership, and identify themselves (or their agents) as authorities ready to enforce their requirements. In addition, buyers will want to ensure that their manufacturers also have strong leadership, ready to take action on the buyer’s behalf when needed.
- Engagement of people: Achieving high-quality production is impossible if the involved personnel are not notified, familiarized, trained, coached and otherwise fully engaged toward the expected quality objectives. A robust QMS makes sure that all parties in component manufacturing know their role and responsibilities for hitting quality targets, both on the buyer’s side to continually beat the drum, and on the manufacturer’s side to follow the beat.
- Process approach: Quality management is a process, executed as a series of steps towards a stated goal. Individual steps can be standardized and executed in a tightly repeatable way for the greatest success. More importantly, following prescribed processes helps catch issues early, saving rework and quality concerns. Buyers should outline their desired processes to manufacturers and should also review manufacturers’ processes for any incompatible steps (such as packaging, finishing, cleaning and load-securing).
- Improvement: Quality cannot be maximized if marginal conditions are not pushed to improve. Improvement can take the form of individual people doing better at their tasks, input resources being better prepared or even machinery and operations being pushed toward higher performance. Buyers should broadcast their expectations that any faltering conditions found during component manufacturing be immediately improved, at no loss to the buyer.
- Evidence: Manufacturing decisions that impact quality should never be made off the cuff. Too many times, quality shortcomings are worked out without proper evaluation, causing unexpected issues or increased costs. A robust quality management system should always be rooted in evidence-based decision making. Additionally, buyers should outline their expectations for notification, collaboration and joint decision-making based on actual evidence.
- Relationship management: In many ways, quality is a negotiated middle ground between buyers and manufacturers where one side wants to maximize customer satisfaction, and the other wants to maximize profits. Which side is which is not always so obvious, nor does it matter. Relationships between buyers and end-users, buyers and manufacturers, manufacturers and suppliers, and so on can all influence this balance when they’re not all measuring to the same expectations. Across a complete supply chain, this means that managing and aligning relationships can be just as important as technical details in component manufacturing, so that everyone understands the interests and needs of all others.
Key Quality Parameters to Pursue
Readers who are not yet able to jump into a full-blown QMS effort might ask which quality parameters are the most critical to focus on upfront.
While every order, buyer, product and manufacturer may be different, from our experience, here are the four quality metrics that we see impacted the most in offshore component manufacturing:
- Unit-to-unit consistency: Some manufacturers are able to produce products within or nearly within a buyer’s specification range, but with a wide variation from one end of the range to the other across a production run. In one way, this can be seen as acceptable as the parts are still within tolerance, but the wide range between the extremes can still create quality concerns (especially client satisfaction concerns).
- High-tolerance defect detection: Too often, manufacturers are able to achieve a high-tolerance product specification, but are not great at measuring and detecting out-of-tolerance conditions at the same level of resolution. Buyers should always prequalify component manufacturers on both their production capabilities as well as their quality control capabilities.
- Non-standardized processes: Manufacturers that do not utilize standardized production processes tend to experience higher variability in their end products. These variances can lead to low-quality end-user experiences, reseller complaints and other issues (including more quality control rejects on the receiving end).
- Reporting reliability: To be frank, some manufacturers are not as diligent or trustworthy in their reporting of issues as we may want them to be. Lower-tier suppliers will often cut their losses on poorly produced runs and ship the units without notifying anyone of issues, leaving buyers to wait for the surprise of unacceptable products when they arrive stateside. For this reason, quality management tools are all that protect a buyer from falling into this trap, be it via the use of robust specifications and communication, or onsite representation and in-process sampling audits.
Your Guide to Component Manufacturing
When you partner with ITI Manufacturing, we help create clear specifications, support transparent communication and provide expert onsite representation. Where could you use help with component manufacturing quality? Contact us today for more information.