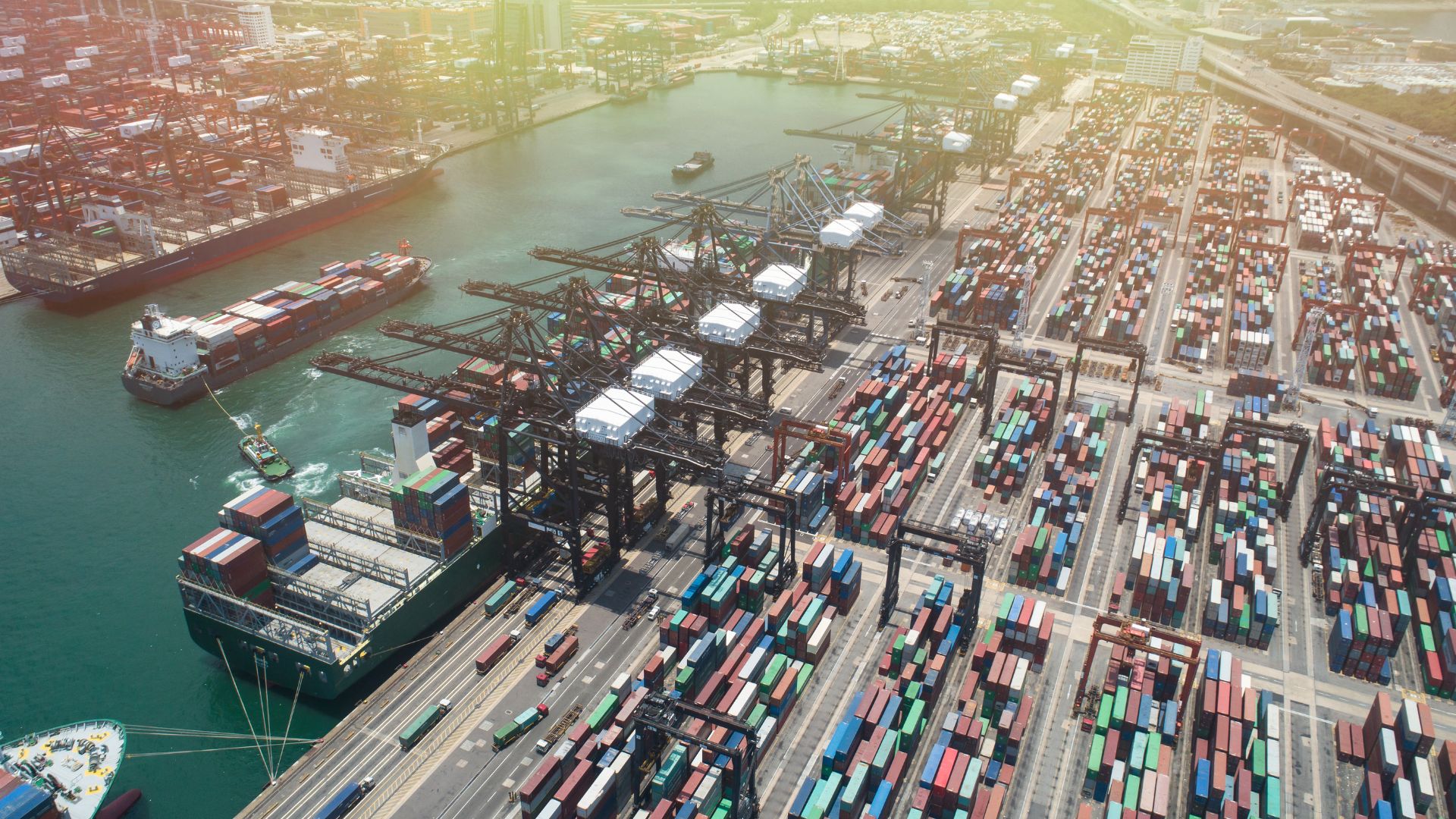
When it comes to modern supply chain planning discussions, there is an overwhelming amount of noise. One topic that’s especially noisy involves choosing supply chain models.
Recently, a few clients asked how we select our own manufacturing models. Answering the question required us to dig down to pertinent specifics. Since this was a helpful process with our own inquiring clients, we want to share the same information here with the broader community.
If you do a web search on “supply chain models,” the top results will likely return a list that looks like this:
- Continuous flow
- Fast chain
- Efficient chain
- Agile
- Flexible
- Custom configured
Some articles generically describe each model but leave much to be desired in the way of concrete details. While these named models may hold some merit from a software standpoint, they fall far short of being actionable by supply chain managers to any useful degree. In an effort to provide real actionable information to supply chain professionals, let’s set this list aside and build a definition of supply chain modeling from scratch.
Supply Chain Modeling: An Analytical Process
To understand the function of supply chain modeling, we need to start at the very top of the overall topic, which would be the academic subject of supply chain management.
Supply chain management refers to the business workflow of controlling all the factors that contribute to delivering commercial products to customers.
Supply chain planning is one step in the process of supply chain management. Through planning, supply chain managers can arrive at a strategic array of material acquisition, manufacturing and distribution decisions that collectively make up their product’s path to market.
When planning supply chains, assembling that plan in the form of a supply chain model provides a quantitative tool that spans all supply chain nodes, stages, performance criteria and interconnecting dependencies (such as logistics and governmental factors). A model is two things simultaneously:
- A list of supply chain facets that have data and metrics assigned to them, allowing projections and statistical analysis to be performed on each data point, driving daily managerial decisions and actions. This list could be tracked through an Excel spreadsheet, a web dashboard, a custom application or even a hand-written document.
- A philosophy based on expertise. For example, a model for a low-cost product would suggest fewer manufacturing steps, commodity material selections and offshore contract assembly. The model would be influenced by what is known to work best with this product type.
Differentiating Supply Chain Model Categories
Now that we understand the concept of supply chain models and how they fit into daily supply chain management, how can we distinguish and categorize different models? At the highest level, we like to split supply chains into one of two categories, drawing from this Harvard Business Review article (downloadable PDF here):
- Efficient supply chain: This framework is mostly used for products having predictable demand levels, where demand can be satisfied at the lowest possible cost, inventory can turn over frequently and suppliers are selected based on cost and quality. Supply chains designed in this category often use fewer manufacturing steps, more commoditized raw materials and more streamlined operations.
- Responsive supply chain: This framework trades the cost minimization features of an efficient supply chain for aggressive performance, built upon minimal lead times, high quality and speed, great flexibility and advanced technologies. Supply chains designed in this category often rely on higher manufacturing diversification, more specialized manufacturing processes, and high flexibility and customization at each step.
How did the HBR article’s author come up with these categories? By seeking to align a supply chain to the product types being distributed. Products were broken down into “functional” and “innovative” categories, and mapped to the appropriate supply chain model as seen in this graphic from the same article:
Let’s put this information into context with an example: A product is manufactured that could be described as a commodity, perhaps a replacement wear part for industrial equipment. While many unique, innovative features are integrated into the design, the product itself is purchased as a functional product (that is, bought on price and lead time, not experience or social trends as seen with innovative products).
This identity suggests that an efficient supply chain type would be the best match for functional products, focusing on cost minimization and ease of access.
Digging Deeper: Arriving at a Final Supply Chain Model
To recap: Managers go through the effort of supply chain planning, focusing on building in strategic benefits that align with their product types, and more importantly, what their customers demand when procuring those products. Putting all of these features and requirements into one place is synonymous with building a supply chain model, which is an analytical tool that managers can use to measure supply chain performance on a daily basis.
Now we can answer the original question: How do we at ITI Manufacturing select a specific supply chain model?
We don’t follow any exhaustive list of preexisting models, per se. Instead, we create bespoke models that provide features that align with the supply chain categories of efficient and responsive. In other words, we solve for cost versus speed.
As you consider supply chain models, it’s crucial to decide on the most important factors using the framework above, and then solve for discrete features that match your branding and commercial needs.
Our top 10 supply chain planning model features are:
- Total cost/efficiency model for products prioritizing the lowest possible cost to produce, likely utilizing offshore manufacturing in developing areas, few or only one manufacturer, and long-run volume pricing agreements.
- Variable demand/responsive model for products with big swings in their demand. Batch-order pricing agreements and multiple qualified manufacturers spread the short-notice order requests around.
- Specialization/responsive model for truly unique products. This model selects manufacturing nodes and partners specifically for their competitive specializations (such as IP, tool processes or materials).
- Resource availability/responsive model for products that require high-value, seasonal or otherwise scarce raw resources, solving for high availability and control over these resources despite the higher costs.
- Sales patterns/efficient model for products with distinct sales patterns (such as bulk orders to wholesalers or seasonal extremes) using batch production to maximize margins across sales cycles.
- Customer demands/responsive model for products that entirely center around customer requirements and expectations, all manufacturing steps must be very nimble and ready to react. Vertical integration is common.
- Social and product trends/responsive model for products that go beyond mere customer demands and seek to blaze the trail in social and cultural trends, usually calling for batch production, high quality and emergent design features.
- Production patterns/efficient model for products that are best manufactured in discrete run cycles, such as with semiconductor products where there are high costs to change over the production line to different SKUs.
- Efficiency and sustainability/efficient model for products that target environmental and energy efficiency, sustainability and low waste. Such supply chains focus on fewer production steps, fewer logistics routes, shorter transit distances and lower resource consumption throughout, making this chain design primarily rooted in lean principles.
- Tax and trade factors/efficient model for products that strategically take advantage of international tariff and domestic tax conditions, supply chain nodes are selected specifically to meet key regulatory criteria
Your Supply Chain PlanningWhat’s best for your product? We can help you make supply chain decisions. Contact us to learn more.