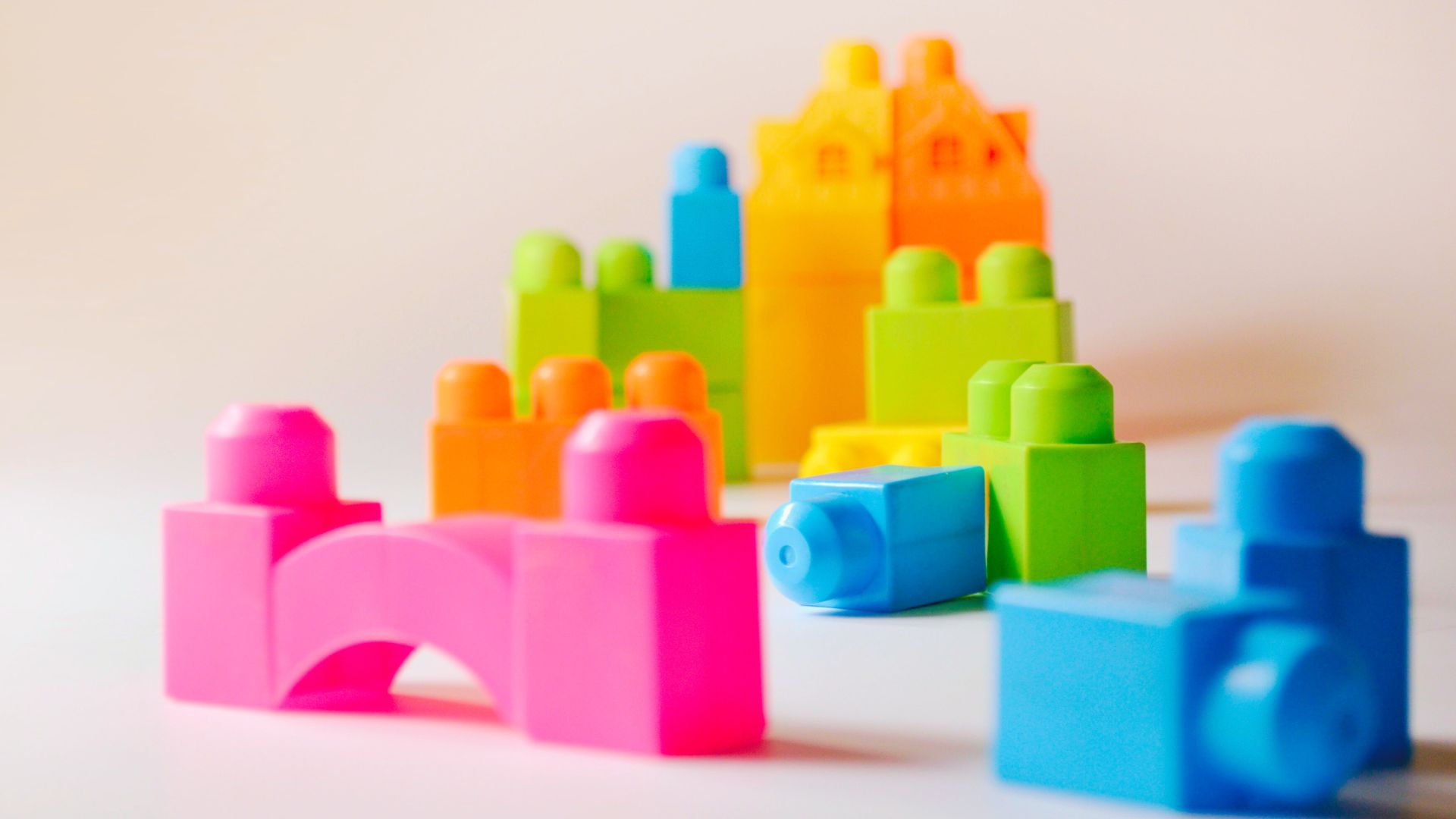
Sourcing custom plastic parts – domestically or via import – is laced with potential complications, stemming from complex engineered materials to even more complex manufacturing methods. What should you keep in mind when sourcing custom manufactured plastic components?
Here’s a close look at the plastic part supply chain process and the information you need to steer clear of complications.
Step by Step
Starting with the overall plastic part supply chain process, most sourcing engagements that we employ for our clients’ custom plastic parts follow these steps:
- Proof of concept. After a new plastic product is designed, a practical manufacturing test is the first step in developing that product’s supply chain. Real material compositions, production process steps, finishing passes and all other actual manufacturing methods are tested out, confirming or augmenting all sourcing decisions to come.
- Manufacturing tender. With a validated production concept in hand, buyers extend formal proposal tenders to qualified suppliers, requesting competitive price and lead time offers for manufacturing services.
- Purchasing. At this stage, buyers review, negotiate and accept a winning supplier proposal for the bulk manufacture of their plastic parts. Both parties exchange the necessary commercial agreements and financial elements, putting real-life production into motion.
- Manufacturing. Once a supplier is released to begin production, they order raw materials, allocate resources and labor, and schedule factory time for the run. At this stage, money and resources begin to be consumed, continuing until the production run is complete.
- Logistics. Per the terms of the procurement agreement, the supplier begins shipping complete or partial plastic unit volumes out to the buyer.
- Distribution and warehousing. Though it varies by company, product shipments tend to route to distribution warehouses for intermediate storage prior to final delivery. Quality inspections, volume counts and technical part testing are often performed upon receipt.
- Sales and delivery. At the end of the supply chain, products are routed to their final destination either through direct or third-party sales efforts. Once products are sold, the products can be dispatched from their warehouse and delivered to end customers.
These steps in the process formulate the building blocks of custom plastic parts manufacturing, but we’ve only just gotten started. The next section is where things start to get interesting.
Structuring Plastic Supply Chains
What mainly sets plastic manufacturing supply chains apart from other products is not the overall supply chain process itself, but instead the nuances within each step specific to plastics. To start breaking down the distinctions of plastic part procurement, we’ll start with differences driven by the plastic materials themselves.
Materials
Plastic manufacturing typically distinguishes materials by these five categories:
- Thermoplastics are plastic materials that become malleable when heat is applied and then solidify when heat is removed. Thermoplastics can be reshaped by subsequent heating cycles, making them highly workable but relatively lower in strength. Acrylic, nylon, ABS, polyethylene, PVC and polycarbonate are examples.
- Thermosets are a group of plastics that start as a semi-solid or liquid resin, then are cured by heat, radiation, pressure or a catalyzing agent to a high level of structural strength. Thermosettting changes the molecular makeup of the polymer, and once set, cannot be remade or reshaped afterward. Epoxies, polyurethanes, esters, polyimides, silicone and vulcanized rubber are examples.
- Textiles include the many fabrics that today are made entirely or partially out of plastic materials. They typically use polymers in the form of synthetic fibers or polymeric additives laced into natural fibers. Polyester, nylon, acrylic, spandex and polypropylene fibers are common examples.
- Elastomers are polymers that are “stretchy.” They have viscoelastic properties where they can be deformed and still return to their original shape at room temperature. Known as elastomers, they are often informally just called rubber. Nitrile rubber, silicone rubber, polyisoprene, Viton and elastolefin are examples.
- Exotics / biodegradables include today’s bleeding-edge material compositions. Biopolymers are a class of polymers stated to be compatible with organic processes, such as being edible. Biodegradable plastics can be decomposed by bacteria, microorganisms or composting.
Methods
Next, let’s have a quick glance at the most common custom plastic parts production methods:
- Extrusion produces continuous profiles, such as plastic tubing and structural shapes.
- Injection molding injects high-temp fluid plastic material into a molded cavity, allowing the material to take on the solid shape of the mold as it cools, such as with electronic housings and medical devices. Injection molding is the most common modern plastic manufacturing method.
- Blow / vacuum molding produces hollow plastic shapes such as plastic containers and bottles by applying gas pressure or vacuum to a preheated plastic parison, expanding the parison out to the shape of the mold.
- Rotational molding relies on rotational force, instead of gas pressure or vacuum, to distribute a preheated polymeric liquid evenly over the surface of a mold. This method is typically used for large molds where gas-assisted molding would be unreliable, such as with large tanks, road cones and helmets.
- Machining involves using traditional tool processes on blocks of raw plastic materials. One of the oldest custom plastic part manufacturing methods, it provides higher tolerance parts but often at a higher cost such as with industrial replacement components and consumable fabrication fixtures.
- Thermoforming produces profiles and shaped products out of preheated flat plastic sheets, where a hot form is physically thrust into the sheet, deforming the sheet to match the form’s profile. Often used for plastic packaging and containers.
- 3D printing is the most recent advancement in plastic manufacturing technologies. Used across a growing number of product types, 3D printing is able to generate part features in any axis and plane. 3D printing’s costs and speeds are constantly improving, though printed parts often need secondary processing.
As you can see, the devil is in the details concerning plastic materials and manufacturing methods. In many cases, a single product will call for multiple tool processes and materials. Such a product might require multiple specialized suppliers and many intermediate supply chain steps (from separate material sourcing to inter-supplier shipping).
Key Considerations for Plastic Parts Procurement
Over decades of first-hand experience, we’ve gained unique insight into the nuances of sourcing manufactured plastic products, especially when engaging foreign suppliers. Below are a few bits of advice that we hope will benefit your next plastic manufacturing project.
- Request manufacturing samples. Nothing beats holding a tactile sample in your hands, personally evaluating it for quality, appearance and function. Drawings and specs can easily be misinterpreted, but a sample can transcend most communication issues.
- Require certificates of conformity. Too often, suppliers may substitute materials, accept shoddy alternatives, source from illegitimate wholesalers or otherwise risk your products due to nonconforming procurement decisions. Certificates of conformity keep the record straight.
- Reference compliance standards in contract. Especially for regulated products, hold suppliers accountable directly to federal, state, industry and advisory standards by including them as a function of the procurement agreement.
- Specify shipment and packaging protection. Plastic parts are generally more sensitive to shipping damage such as abrasion, temperature deformation, indentation and even collapse if piled under heavy weights. Lay out precise shipment requirements to assure everything arrives as intended (or better).
- Be explicit with quality requirements. Consider these two product quality requirements: “ensure a smooth outer finish” is not the same as “provide a continuous outer surface roughness of Ra<16, grained in a uniform direction parallel to the part’s length axis, with solvent rinsing to remove all foreign matter”. Be clear so as to avoid surprises.
Your Next Custom Plastic Parts Project
Let us put our decades of experience with custom plastic parts manufacturing to work for you. Contact us today with your questions or to get more information about our processes.