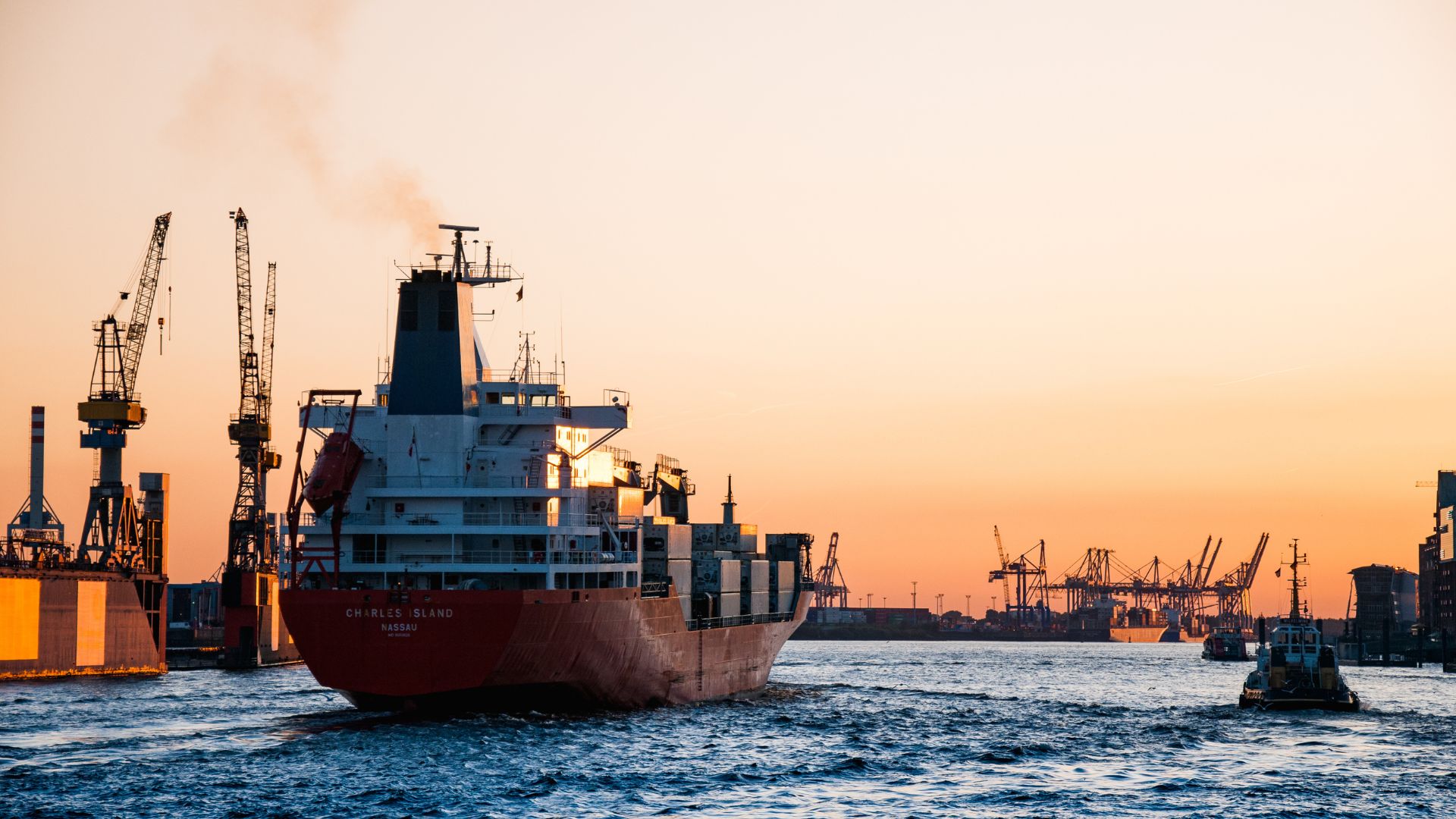
To produce a highly desirable, well-made product, manufacturers must assemble a team of suppliers that bring the most value to the table. Selecting these suppliers can be a heavy burden, especially when the manufacturer is located in a region where the specialized knowledge and technologies needed are in short supply. This requires the manufacturer to cast a wide net, one that often leads overseas.
Foreign suppliers offer an irresistible combination of costs and capabilities based on their local economic conditions and access to resources, driving manufacturers to engage that supplier to assume portions or all of the manufacturer’s production workflow.
This concept of delegating entire business operations to foreign suppliers is known as offshoring, and today this is one of the main ways that manufacturers chisel out their competitive advantage.
Offshore manufacturing is no magic bullet as it comes along with just as many potential risks as it does opportunities, which we’ll discuss in detail below.
First, let’s define offshore manufacturing.
What is offshoring?
Offshoring refers to moving any business operation wholly to a foreign nation, away from the country that the business originates from.
These offshore operations can be directly owned by the company, or they can be created through contractual engagements with separate entities.
Why would a business choose offshore manufacturing?
Businesses choose offshore operations to take advantage of opportunities found within these foreign markets such as access to scarce resources, low costs, and unique specializations.
Businesses may also offshore operations to skirt regulatory, legal, or social constraints found back home.
Where Offshore Manufacturing Shines Bright
Offshore manufacturing can be a lucrative solution to local constraints, providing benefits such as:
Cost Optimization
Developing foreign economies can offer substantially lower labor and material costs compared to a manufacturer’s home country (especially western countries), and offshoring allows manufacturers to directly improve their bottom line by tapping into these lower costs.
Proximity to Resources
Offshoring to regions of the world where the resources needed for a manufacturer’s products are abundant can directly cut the associated procurement costs as well as improve the reliability of obtaining that resource.
Access to Talent
Manufacturers may choose to offshore production to regions of the world where specific talent pools are highly available, such as India for IT talent or Vietnam for machinery assembly talent.
Geographic Advantage
Major manufacturers must balance geographic concerns involving their proximity to shipping channels, buyer markets, and production resources. Very few places in the world can provide perfect access to all three, so offshoring offers a way to separately locate business elements where they can provide the most value.
Commercial Alliance
Often, there are key commercial advantages to be gained through partnering with reputable offshore suppliers, such as mutual investment in the supplier’s production efficiency, quality, and reliability. In addition, offshore suppliers can facilitate sales opportunities and local recognition of the manufacturer’s products in their regions.
Government Stimulus
Many countries’ governments offer incentives for offshore manufacturing engagements, including subsidizing costs, providing tax advantages, and even injecting stimulus or grant funds into a transaction.
Regional Specializations
Certain regions have invested heavily in their manufacturing infrastructure to the point that they offer key technology and capability specializations. Examples include Mexico for automotive manufacturing and Bangladesh for textile manufacturing.
Greener Pastures
Sometimes, manufacturers wish to offshore for less tangible reasons, such as for sustainability, trade policy alignment, cultural attributes, and even philosophical interests. In all cases, manufacturers may look to greener pastures that provide something that they cannot achieve domestically, such as offshoring to Germany for their renewable energy benefits or to Ukraine to offer geopolitical support.
Where Offshore Manufacturing May Fall Short
While the above list of positive offshoring features may seem like a surefire path to success, we would be remiss to leave out offshoring’s potential downsides, which include:
Integration Constraints
Foreign suppliers are exactly that – foreign – which may present a number of barriers to full integration of business practices such as language constraints, cultural differences, legal and regulatory factors, and even time zone differences.
Diminished Control
Manufacturers that offshore production to foreign companies must inherently give up a portion of their control over production, quality, performance, and delivery timing. This can lead to blind spots, bad decision making, or worse.
Lead Times and Logistics
The cost benefits of far-off suppliers can quickly be wiped out by slow responsiveness, extended transportation times, added insurance premiums, and shipping damages involved with getting products stateside.
Competitive Attrition
Engaging outside entities requires an extreme level of trust backed by resilient legal and commercial instruments to protect the manufacturer from training a supplier on sensitive production methods, only to have them handed over to competitors.
Intellectual Property Protection
Manufacturers provide their offshore suppliers with incredible insight into the company’s intellectual property, including technical designs, custom tooling, and proprietary workflows which the supplier can easily steal or transfer for their own benefit.
Quality Control
Low-cost offshore suppliers may not possess sophisticated quality control, integrity, or reliability systems as would be expected of western manufacturers, and this can quickly lead to low quality product outcomes if not managed appropriately.
Geopolitical Turmoil
Many developing countries experience heightened political, military conflict, and other diplomatic breakdowns that can threaten a manufacturer’s offshore production activities.
Trade Policy Implications
Just as we’re currently seeing with China, trade policy changes driven by both domestic and foreign governments can over time turn a favorable export country into an unfavorable one. Changes in trade agreements, tariffs, regulations, import inspections, and retaliatory restrictions can result in delays, skyrocketing costs, dissolved contracts, and other issues.
Even in the face of these challenges, many businesses find offshore manufacturing to be a beneficial solution to their unending competitive and cost efficiency demands.
For 50 years, ITI Manufacturing has been a trusted partner for successful offshore manufacturing. We treat each shipment with the utmost care, guaranteeing products free from manufacturing defects. Our commitment to superior customer service and support sets us apart.
Ready to experience the ITI difference? Contact us today and let’s discuss your manufacturing needs.